Job Description
PSM Coordinator
Hourly- $23.50-$26.50
Maintains and operates the Ammonia refrigeration system and associated equipment, boilers, hot water heaters, roof top HVAC units, air compressors, O-zone generation equipment, water softening equipment, backup generator, and fixed fire suppression systems in accordance with all established safety procedures, as well as Company Policy and state and federal regulations and codes. Under supervision, performs semi-specialized tasks in the maintenance of the general plant and/or office building in the skill areas of plumbing, carpentry, painting, cement applications, door repairs (personnel and industrial), maintains building lighting, rooftop ventilation units, fire sprinkler piping repairs, building electrical, and utilities Monitors, adjust, and maintains the wastewater system and coordinates the repairs of wastewater system components including cleaning, troubleshooting, electrical and mechanical repairs. Understands, troubleshoots, and repairs of all previously stated equipment and systems. Conducts maintenance daily checks, logs and readings on previously stated equipment and systems. Performs preventive and corrective maintenance on previously stated equipment and systems as assigned to maximize uptime and operating efficiency. Identifies all parts, supplies, and services required to maintain assigned areas and shifts. Conducts routine inspections of walls, floors, ceilings, insulations, piping, roof, parking lot, wastewater system, etc. Performs minor electrical maintenance to include but not be limited to replacement or repair of fixtures (e.g. wall switches and outlets, incandescent and fluorescent bulbs and tubes, ballast, sockets, fuses, minor appliances, cords, etc.) using appropriate hand, power and specialty tools. Replaces or updates inoperable or old building materials and appliances (e.g. motors, belts, pumps, window glass, sinks, doors, smoke alarms, cabinets, shelves, tile, light fixtures, filter systems, patios etc.) to provide a safe, comfortable working environment for employees using various tools and materials (e.g. welding equipment, ladders, power saws, hammers, drills, etc.).
Maintenance
Maintains and operates the Ammonia refrigeration system and associated equipment, boilers, hot water heaters, roof top HVAC units, air compressors, O-zone generation equipment, water softening equipment, backup generator, and fixed fire suppression systems in accordance with all established safety procedures, as well as Company Policy and state and federal regulations and codes. Under supervision, performs semi-specialized tasks in the maintenance of the general plant and/or office building in the skill areas of plumbing, carpentry, painting, cement applications, door repairs (personnel and industrial), maintains building lighting, rooftop ventilation units, fire sprinkler piping repairs, building electrical, and utilities Monitors, adjust, and maintains the wastewater system and coordinates the repairs of wastewater system components including cleaning, troubleshooting, electrical and mechanical repairs. Understands, troubleshoots, and repairs of all previously stated equipment and systems. Conducts maintenance daily checks, logs and readings on previously stated equipment and systems. Performs preventive and corrective maintenance on previously stated equipment and systems as assigned to maximize uptime and operating efficiency. Identifies all parts, supplies, and services required to maintain assigned areas and shifts. Conducts routine inspections of walls, floors, ceilings, insulations, piping, roof, parking lot, wastewater system, etc. Performs minor electrical maintenance to include but not be limited to replacement or repair of fixtures (e.g. wall switches and outlets, incandescent and fluorescent bulbs and tubes, ballast, sockets, fuses, minor appliances, cords, etc.) using appropriate hand, power and specialty tools. Replaces or updates inoperable or old building materials and appliances (e.g. motors, belts, pumps, window glass, sinks, doors, smoke alarms, cabinets, shelves, tile, light fixtures, filter systems, patios etc.) to provide a safe, comfortable working environment for employees using various tools and materials (e.g. welding equipment, ladders, power saws, hammers, drills, etc.).
Process Safety Management (PSM)
• Manage the Management of Change (MOC) process.
• Coordinate and ensure all PHA's are performed as required.
• Ensure PSM program is always audit ready.
• Ensure monthly PSM team meetings are held and documented with meeting minutes.
• Participate in a 3-year PSM Compliance Audit at another facility at least once every three years.
• Ensure follow up tracking is documented on all PHA recommendations to closure.
• Ensure follow up tracking is documented on all Compliance Audit "Exceptions" and "Other Corrective Actions".
• Schedule and coordinate quarterly updates the facility manager and affected employees on all PHA open items.
• Schedule and coordinate quarterly updates to the facility manager and affected employees on all Compliance Audit open Exceptions and Recommendations.
• Schedule and coordinate quarterly updates to the facility manager and affected employees on all Mechanical Integrity Inspection open defects.
• Ensure proper preventative maintenance procedures are written with detailed long text and revised as necessary on all ammonia equipment.
• Ensure operating procedures are written on all ammonia equipment and are maintained current and accurate and updated as often as necessary.
• Ensure operating procedures are certified annually to be current and accurate. Assist in environmental issues related to the Ammonia Refrigeration System. Provide PSM leadership across all shifts in establishing, organizing, planning, and implementing PSM program and corporate ammonia initiatives.
• Ensure Refrigeration Operators are trained, and training is documented according to the Training Element and site-specific Training Total Curriculum.
• Revise the facility PSM program according to Kraft Heinz Corporate PSM Team revisions that are sent out periodically.
• Ensure appropriate PSM documentation and procedures (i.e. MOC, Line Break, and PHA) are followed on all ammonia projects.
• Coordinate associated ammonia best practices across the plant and facilitate continuous improvement in the Utility group.
• Attend the annual Kraft Heinz Ammonia Safety & Best Practices Workshop. Network with the Kraft Heinz PSM Team to remain aligned, up to date on information, and current on the direction being shared across all Kraft Heinz ammonia refrigeration facilities.
• Have access to up to date "Recognized and Generally Accepted Good Engineering Practices."
• For Ammonia Refrigeration, this is the International Institute of Ammonia Refrigeration (IIAR)
• Associate Membership in the IIAR provides full access to all IIAR Codes & Standards
• Membership can be established after placement in the role of PSM Coordinator
Reporting
Updates Computerized Maintenance Management System (CMMS) in support of Preventive & Corrective Maintenance. Participate in monthly Corporate PSM Coordinator conference calls.
Safety
Ensures a safe and sanitary work environment at all times while following established safety regulations in the performance of all job tasks and reporting any unsafe conditions immediately. Adheres to the Process Safety Management (PSM) / Risk Management Program (RMP) and Hazardous Waste Management Programs related to the ammonia refrigeration system to ensure compliance with city, state, and federal environmental regulations. Complies with environmental regulations, Good Manufacturing Practices (GMP) and the plant's Maintenance Safety Programs. Assist facility ORM in managing the Hot Work Program and Emergency Action Plan.
Control Costs
Completes work orders in a timely manner meeting or exceeding pre-established deadlines to reduce downtime and meet production goals. Ensures all quality standards are met or exceeded. Recommends changes established manufacturing processes to reduce or eliminate down time, increase operational effectiveness, and improve routine maintenance in all assigned areas and shifts.
Internal Customer Service
Works with Production Department to determine optimal time for any needed repairs on equipment. Follows through to ensure repairs are made on schedule. Informs Production Supervisor and Maintenance Supervisor of any issues. Establishes positive working relationships with all plant personnel.
Qualifications
EPA Section 608 Universal Certification maintained Certification of Qualification on the Delimex ammonia refrigeration system, CO2 system, PSM process and facility SOP's Understanding of steam principles and facility steam systems with the ability to troubleshoot pumps, valves, piping and water treatment General knowledge of the plant air system, water system, and Fire Protection System
Quality
Interprets and takes ownership of GMPs and food safety company standards. Must be able to provide recall information for raw material usage as well as disposals. Coordinate with Quality Assurance on any product placed or released from hold status, raw materials as well as finished product. Participate in the QRMP yearly audit and assist in the development of procedures and corrective actions. Accountable for the QRMP (Quality Risk Management Process) system and operational standards as outlined in the plant accountability list in order to achieve targeted RCR.
Manufacturing Playbook
Participates in the implementation of the factory's playbook, especially in the pillar assigned to the department, to ensure successful completion of all checklist items/actions within the playbook.
The preceding functions have been provided as representative of the types of work performed by the employees assigned to this job classification. Management reserves the right to add, modify change or rescind the work assignments of this and different positions and to make reasonable accommodations so that qualified employees can perform the essential functions of the job.
KNOWLEDGE / SKILL / EXPERIENCE LEVELS
The Refrigeration Technician must possess knowledge of and understand the following:
- Basic maintenance principals regarding refrigeration, HVAC, compressed air, water, steam, gas, oil, chemical, and fire protection systems.
- HAZMAT, PSM, RMP, OSHA regulations, plant Maintenance Safety Program, and GMPs affecting all aspects of PM/CM safety within the plant and facilities.
- Understanding of steam principles and facility steam systems with the ability to troubleshoot pumps, valves, piping and water treatment.
- Policies, procedures, methods, and processes for performing preventive maintenance in assigned area(s) of responsibility.
- Measures to improve production efficiency, equipment performance, product quality, and plant safety.
- Parts and supplies required to support assigned areas and shifts.
- Plant's quality standards, policies and procedures.
The Refrigeration Technician must possess the following skills:
- Operate the ammonia refrigeration in accordance with all established safety procedures, codes, and regulations.
- Diagnose malfunctions/hidden defects in equipment and machinery and repair of all assigned equipment previously mentioned.
- Read wiring diagrams, blueprints, schematics, and manuals and logs.
- Basic welding (Stick, MIG, TIG, Soldering/Brazing).
- Enter data into CMMS.
- Update maintenance logs.
- Implement measures to improve routine maintenance, production efficiencies, operational effectiveness, equipment performance, and safety in all assigned areas and shifts.
The Refrigeration Technician must possess the following minimal education and experience:
- High School Diploma.
- HVAC Certification through an accredited vocational school. EPA Section 608 Universal Certification maintained
- Understanding of steam principles and facility steam systems with the ability to troubleshoot pumps, valves, piping and water treatment.
- General knowledge of the air systems, water systems, and Fire Protection Systems.
Preferred
- Three (3) years of experience in the refrigeration Food Industry and ammonia refrigeration.
- Basic welding certification through accredited vocational school.
Benefits: Coverage for employees (and their eligible dependents) through affordable access to healthcare, protection, and saving for the future, we offer plans tailored to meet you and your family's needs. Coverage for benefits will be in accordance with the terms and conditions of the applicable plans and associated governing plan documents.
Wellbeing: We offer events, resources, and learning opportunities that inspire a physical, social, emotional, and financial well-being lifestyle for our employees and their families.
You'll be able to participate in a variety of benefits and wellbeing programs that may vary by role, country, region, union status, and other employment status factors, for example:
- Physical - Medical, Prescription Drug, Dental, Vision, Screenings/Assessments
- Social - Paid Time Off, Company Holidays, Leave of Absence, Recognition, Training
- Emotional - Employee Assistance Program , Wellbeing Programs, Family Support Programs
- Financial - 401k, Life, Accidental Death & Dismemberment, Disability
Location(s)
Delimex - Hourly
Kraft Heinz is an Equal Opportunity Employer that prohibits discrimination or harassment of any type. All qualified applicants are considered for employment without regard to race, color, national origin, age, sex, sexual orientation, gender, gender identity or expression, disability status, protected veteran status, or any other characteristic protected by law. Applicants who require an accommodation to participate in the job application or hiring process should contact [email protected] .
Top Skills
What We Do
Kraft Heinz is a global food company with a delicious heritage.
With iconic and emerging food and beverage brands around the world, we deliver the best taste, fun and quality to every table we touch.
We’re on a mission to disrupt not only our own business, but the global food industry. A consumer obsession and unexpected partnerships fuel our progress as we drive innovation across every part of our company.
Around the world, our people are connected by a culture of ownership, agility and endless curiosity. We also believe in being good humans, who are working to improve our company, communities, and planet.
We’re proud of where we’ve been – and even more thrilled about where we’re headed – as we nourish the world and lead the future of food.
Why Work With Us
We believe that great people make great companies, and we’re growing something great here at Kraft Heinz.
Operating in over 20 global markets, across 9 functions, no matter your career goals, we have a seat at the table for you.
Gallery
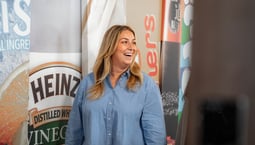

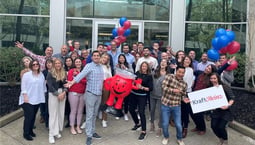
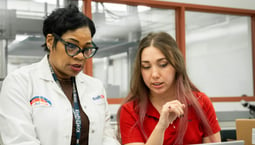
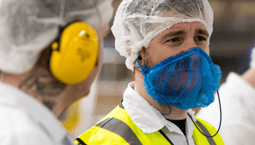

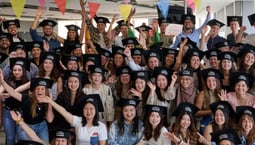
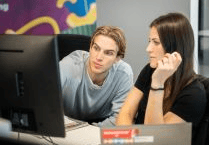
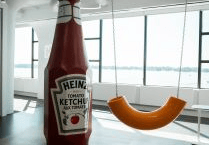
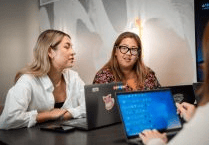
Kraft Heinz Offices
Hybrid Workspace
Employees engage in a combination of remote and on-site work.
We also believe providing a more flexible and agile model is essential in today’s workplace. A majority of our office-based employees will be able to work remotely for up to two days each week.