What we offer:
At Magna, you can expect an engaging and dynamic environment where you can help to develop industry-leading automotive technologies. We invest in our employees, providing them with the support and resources they need to succeed. As a member of our global team, you can expect exciting, varied responsibilities as well as a wide range of development prospects. Because we believe that your career path should be as unique as you are.
Group Summary:
The Magna Exteriors portfolio of products includes access systems such as liftgates, exterior trim, modular systems, front-end modules including fascia, active aerodynamic systems and other lightweight structural components for automotive, commercial truck and other industrial markets.
Recognized globally as an innovator in all aspects of vehicle exteriors, Magna provides everything needed, from materials development and design through manufacturing and assembly, to help automakers create sleek, state-of-the-art vehicles across the world.
Job Responsibilities:
General Job Duties:
- To exhibit an objective, fair and professional attitude that exemplifies the principles outlined in The MAGNA Employee's Charter to maintain a positive and productive workplace.
- To follow Decostar policies and display conduct expected of Decostar employees as described in the employee handbook.
- Ensure that you follow company policies and business objectives in the daily supervision of the operations of the company.
- To exhibit teamwork and leadership skills and actively participate in team activities in a positive working environment.
- To demonstrate problem solving skills in a work environment that is striving for continuous improvement.
- To support all customer quality standards as well as the standards of Decostar.
- To perform daily cross-functional job assignments as required and per the department's established procedures and work instructions.
- Ensure a spirit of respect, cooperation, ethical conduct and fair dealing in all our operations between our internal, external customers and suppliers.
Specific Job Duties:
- To direct and follow Decostar Industries health and safety policies and procedures that provide for a safe and healthful workplace for all Decostar Industries employees, contractors and visitors.
- Exemplify the Charter principle for a safe and healthful workplace by correcting unsafe behaviors, eliminate or reduce the possibility of an employee injury due to hazardous conditions.
- Immediately respond, in a positive and proactive manner to any Decostar employee's health and safety concern or suggestion.
- Immediacy report any accidents, incidents or near misses to the Safety Department and complete the required Accident Reporting Forms within 24 hours.
- Complete all required safety-related inspections.
- Do not install or make changes to any equipment or machinery that may jeopardize the health and safety of any employee.
- Ensure all employees, under your guidance, have received all required training to perform their job safely
- Exemplify the Charter principle for a safe and healthful workplace.
- Demonstrate awareness for the safety of others in the work environment.
- Integrate safety into all element of the organization.
- Make every effort to eliminate hazardous conditions and practices.
- Inspect examination of workplace condition to ensure they conform to applicable standards.
- Demonstrates commitment and support personnel to reducing the impacts of its operation on the environment.
- To Understand the employee's rights under the OSHA Act, EEOC, FLSA and do not allow for discrimination against any employee exercising their rights.
- Always use appropriate Personal Protective Equipment to set good workplace standards and ensure all employees maintain those standards.
- To follow safety rules of Decostar and work in a manner that is conducive to maintaining a safe and healthful workplace including: training of new employees, reporting unsafe acts or conditions and correcting or commending health and safety performance.
- Ensure that all accidents or injuries are reported immediately and actively participate in the accident investigation and completion of all open action items.
- Have knowledge of general workplace health and safety in regards to the general public and visitors to Decostar.
- Develop the program execution plan under the guidelines of the Advanced Product Quality and Planning (APQP) process.
- Define customer needs and expectations for assigned programs. Establish customer milestones from design to production readiness. (Production readiness is defined as developing parts capable of being manufactured by each department at the quoted performance parameters for material labor and overhead utilization.)
- Represent the internal manufacturing departments when working with the Account Manager, to meet or exceed customer expectations through resolving product related OEM issues.
- Create and maintain a master timeline that details internal and supplier execution deadlines required to meet customer milestones. Implement adequate scheduling to allow for tooling modifications to produce a quality product that will meet or exceed customer expectations for sample submission and prototype parts that are delivered on time.
- Maintain tooling costs within budget. Supports requests for quote packages to potential suppliers and complete a competitive analysis prior to awarding business. Use the Decostar Tooling Manual, engineering drawings and math data as a guideline for quoting.
- Participate in a cross-functional team for source selection after analysis of potential suppliers has been completed. Work with Product Engineer to ensure work orders and or purchase requisitions are generated. Ensure suppliers' purchase orders are processed within budget and without delay.
- Work with manufacturing Engineers to ensure secondary tooling is defined specifically for its end use. Ensure quality performance of secondary tooling that meets or exceeds expectations for synchronous manufacturing, ergonomics, environmental and safety standards.
- Maintain product information sheets including: Prototype and Pre-series part delivery schedules, parts building plans, product timelines, Supplier and Customer part history, Customer and Decostar APQP Processes.
- Responsible for all requirements for customer Pre-Production order including control and inspection of products prior to shipment, purchase order tracking, etc. (up to and including Pre-series parts).
- Participate in and present information and/or data as required at customer initiated meetings.
- Maintain an up-to-date Open Issues tracking report of activities inside and outside of APQP Team (using established format). Identify, follow-up on and assign follow-up responsibilities for all action items requiring completion to successfully meet deadlines.
- Provide cost and timing information for all engineering changes on assigned programs, as required. Analyze costs with Product Engineer and Purchasing department, evaluate cost breakdowns prior submission to Customer. Provide all technical information for new tools and Engineering changes to ensure that Customer's required breakdowns and explanation packages are met and delivered on time. When released, follow-up and ensure changes are implemented correctly and on budget.
- Assist Account Manager in providing technical and engineering information and history of new tooling and Engineering changes when required.
- Communicate status of assigned programs on a frequent basis through the Open Issues tracking and APQP tracking documents.
- Maintain controlled documents according to TS 16949/QS-9000 procedures.
- Ensure all required customer APQP sheets are consistently provided on a timely basis according to customer's demand and established APQP process.
- Establish and support positive relationships with suppliers. Develop timelines for tooling and sample part submissions allowing for adequate timing to correct any fit and finishes issues prior to PPAP submission dates of Tier 2 programs.
- Direct and support Supplier Quality Engineer and Product Engineer for supplier activities including fine tuning of supplier product and PPAP submissions.
- Ensure that Production Managers and Team Members are up-to-date on the product's phases, involved and informed about the product challenges, participating in product change decisions and receiving the required support and training during start-up phases.
- Conduct regularly scheduled APQP Launch Presentation on assigned programs to communicate Open Issues concerns to Decostar staff (content will include project information, costs, timing, manufacturing and quality issues).
- Conduct kick-off meeting for Engineering changes on assigned programs and/or new tools. Ensure all required information is available and prepared by the Product Engineer for the kick-off meeting.
- Prepare, update and maintain Customer 'Status Meeting" information.
- Ensure customer's requests and demands are addressed in a timely manner.
- Ensure that design, planning, implementation and closure processes are conducted properly and completed on time. This includes development of the scope of work and the management of time, cost, risk, communication and quality within the company.
- Ensure involvement of manufacturing department in design reviews prior to customer release.
- Ensure the Design, DFMEA, GD&T Product Engineering and PPAP submission conform to the company quality system procedures.
- Ensure all materials are approved and released within the Customer's system.
- Manage the planning for trials during Prototype and Pre-series phases. Establish work priorities and schedules.
- Ensure that all equipment and tooling are transferred on time, parts are properly manufactured and painted, that parts are CMM measured and shipped to meet customer's delivery dates and PPAP submission requirements.
- Ensure DVP&R and testing plans are coordinated with appropriate Supplier.
- Ensure that all part information and BOM details are entered into Decostar's system, confirm that information is accurately entered.
- Utilize APQP and PPAP processes for automotive part submission as required for QS- 9000/TS 16949 certification.
- Act as a Team Leader and participate in team activities as required for the successful execution of required action plans for the launch of assigned programs.
- Perform other duties as directed.
- Have knowledge of your responsibility regarding health and safety in the workplace and be able to communicate the existence of any potential or actual danger to the employee including setting and maintaining clear, written goals.
- Understand the employee's rights under the OSHA Act and do not allow for discrimination against any employee exercising their rights.
- Cooperate with OSHA/State OSHA inspectors.
- Always use appropriate Personal Protective Equipment to set good workplace standards and ensure all employees maintain those standards.
- Know and maintain the safety rules for Decostar Industries.
- Have knowledge of general workplace health and safety in regards to the general public and visitors to Decostar.
Skills and Experience Required:
- Minimum five years experience in design or engineering of automotive exterior decorative trim.
- Ability to plan, schedule, problem solve, delegate, coach, train.
- Minimum two years of experience in managing technical personnel and complex activities. These experiences should be gained in areas of research and development, product engineering, design engineering or technical management.
Education:
- Bachelor's Degree in Engineering required.
Awareness, Unity, Empowerment:
At Magna, we believe that a diverse workforce is critical to our success. That's why we are proud to be an equal opportunity employer. We hire on the basis of experience and qualifications, and in consideration of job requirements, regardless of, in particular, color, ancestry, religion, gender, origin, sexual orientation, age, citizenship, marital status, disability or gender identity. Magna takes the privacy of your personal information seriously. We discourage you from sending applications via email to comply with GDPR requirements and your local Data Privacy Law.
Worker Type:
Regular / Permanent
Group:
Magna Exteriors
Top Skills
What We Do
We are a mobility company that innovates like a start-up and thinks like a technology company. This helps us anticipate change in one of the most complex industries in the world and respond quickly. We depend on a team of 171,000 dynamic, entrepreneurial-minded employees in an environment where great ideas flourish. Our presence spans 343 manufacturing operations and 88 product development, engineering and sales centers in 29 countries.
We understand that you need a career as unique as you are. Whether you want to advance your existing expertise or try something completely different, we are committed to your growth.
Why Work With Us
At Magna, our engineering team is advancing mobility for everyone and everything. Joining this team means being a part of the design, development, and manufacturing of the world’s most advanced mobility technology. Innovations that move families, shape communities, and improve lives. You can follow your passions and shape your own career path.
Gallery
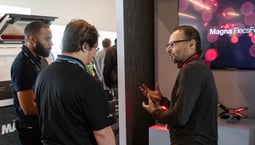
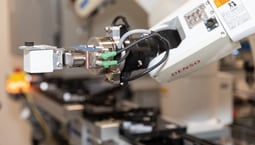
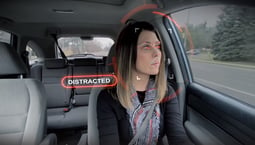
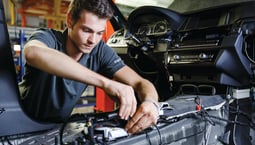
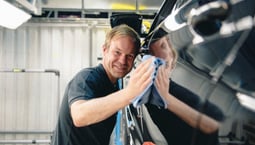
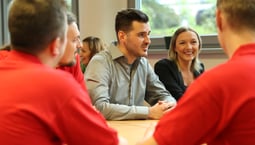
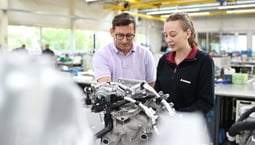
Magna International Teams
Magna International Offices
Hybrid Workspace
Employees engage in a combination of remote and on-site work.
Majority of roles are hybrid with flexibility. Please speak with our recruiting team for specific details on hybrid work.