Job Description
Process Owner
This position is responsible for supervising the production processes and the fulfillment of the key performance indicators of the operation by managing staff on the shop floor and coordinating resources.
Key Accountabilities
Leads production team in achieving production goals around Safety, Quality, Service and Cost.
Ensures compliance to quality systems, Golden Rules, product specifications, process instructions, safety requirements and company policies. Includes the diligent management of non-conformances to ensure appropriate corrective and preventive actions.
Hires, trains, develops and evaluates production personnel to ensure the appropriate resources and talent are in place.
Ensures all production reports are up to date and accurate. Utilizing the data for continuous improvement and recommendations.
Manages and leads production projects from start to completion, ensuring projects are completed in a timely manner.
Monitors daily work metrics and provides direction and guidance to achieve goals and troubleshoot work problems with employees; convey a sense of urgency and drive issues to closure.
Evaluates team member's performance as well as development opportunities on a regular basis of performance review.
Participates in developing new procedures and processes to improve manufacturing or introduce new products.
Creates, routes, collaborates and approves document change orders that affect production documentation.
Oversee daily factory production ensuring that handover from shift to shift is carried out in an efficient manner especially in relation to handoff of shortages and maintenance issues.
Identify and manage the conflicts in the production lines promoting teamwork, communication, empathy as part of adequate organizational environment.
Perform the approval hours, over time, vacation, etc every week to ensure the correct payment to employees.
Participate in HACCP Team. R esponsible for supervising the production processes and the fulfilment all the requirements for the correct implementation of the HACCP Program.
Knowledge & Experience
Education: University degree the areas of engineering, industrial production, administration or the like qualify you for the position desirable.
Experience: Desirable 2 years minimum experience as a Manufacturing Supervisor experience in food or medical industry, managing people, HACCP and ISO standard.
Languages: English (80% desirable), Spanish
Location(s)
San Jose, Costa Rica Plant
Kraft Heinz is an Equal Opportunity Employer - Underrepresented Ethnic Minority Groups/Women/Veterans/Individuals with Disabilities/Sexual Orientation/Gender Identity and other protected classes.
Top Skills
What We Do
Kraft Heinz is a global food company with a delicious heritage.
With iconic and emerging food and beverage brands around the world, we deliver the best taste, fun and quality to every table we touch.
We’re on a mission to disrupt not only our own business, but the global food industry. A consumer obsession and unexpected partnerships fuel our progress as we drive innovation across every part of our company.
Around the world, our people are connected by a culture of ownership, agility and endless curiosity. We also believe in being good humans, who are working to improve our company, communities, and planet.
We’re proud of where we’ve been – and even more thrilled about where we’re headed – as we nourish the world and lead the future of food.
Why Work With Us
We believe that great people make great companies, and we’re growing something great here at Kraft Heinz.
Operating in over 20 global markets, across 9 functions, no matter your career goals, we have a seat at the table for you.
Gallery
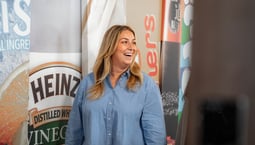

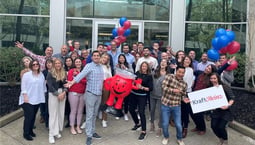
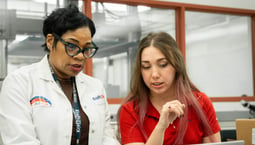
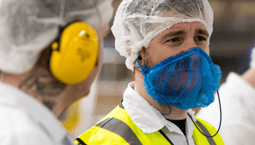

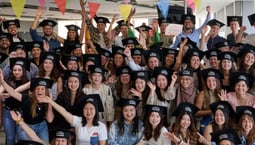
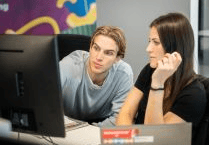
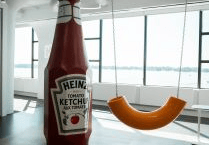
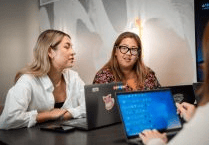
Kraft Heinz Offices
Hybrid Workspace
Employees engage in a combination of remote and on-site work.
We also believe providing a more flexible and agile model is essential in today’s workplace. A majority of our office-based employees will be able to work remotely for up to two days each week.