General Description:
The Manager of Prototype Machine Shop, will be responsible for managing the operations of our prototype machine shop, ensuring optimal efficiency, and utilizing data-driven strategies to improve processes. The ideal candidate will have a strong background in data analysis, machine shop operations, and a passion for driving operational efficiency in a fast-paced, high-tech environment.
The individual in this role will lead a dynamic team of experienced union machinists to produce high quality parts and assemblies on-time and utilizing procedures, metrics, continuous improvement, and other business tools to manage a prototype machine shop and support HRL’s business objective. The ideal candidate must be a self-starter with strong attention to detail, great follow-through, and work with minimal executive supervision.
Essential Duties:
Lead a team of machinists, providing guidance, mentoring, and professional development. Foster a culture of teamwork, accountability, and continuous improvement
Oversee day-to-day activities in the prototype machine shop, including managing the team, workflow, and schedule to meet project timelines
Develop and manage budgets for machine shop operations. Monitor costs, identify opportunities for cost-saving measures, and optimize spending while maintaining quality
Oversee the capital budgeting process, including the analysis, planning, and procurement of new equipment, tools, and technologies required for evolving production needs.
Manage the shop’s budget for investments in machinery, infrastructure, and tools, ensuring that spending is aligned with strategic objectives.
Develop business cases for capital expenditures, evaluating both short- and long-term financial impacts
Develop and implement long-term strategies to position the machine shop for sustainable growth, focusing on increasing production capabilities, improving efficiency, and adopting cutting-edge technologies
Leverage data analysis tools and techniques to track machine performance, production costs, lead times, and resource utilization. Implement continuous improvement initiatives to maximize operational efficiency and minimize waste
Collaborate effectively with senior management to align machine shop operations with overall business goals, ensuring that the shop supports key product development milestones and innovation objectives.
Collect, analyze, and report on production and performance data to identify trends, inefficiencies, and areas for improvement. Use data insights to support strategic decision-making
Work closely with the engineering and research teams to understand prototype requirements, provide feedback on manufacturability, and ensure high-quality prototype production
Oversee inventory management, including ensuring the appropriate materials, parts, and equipment are available for production. Manage ordering and restocking processes to maintain an optimal inventory level
Ensure prototypes meet all technical specifications, quality standards, and safety regulations. Implement quality control processes and inspections
Ensure compliance with safety protocols, environmental regulations, and workplace best practices
Stay abreast of emerging technologies (e.g., 3D printing, robotics, AI-driven automation) and evaluate their potential to enhance shop capabilities, quality, and competitiveness
Required Skills:
Minimum of 7 years of experience in a machine shop environment, with at least 3 years in a management role
Hands-on experience with CNC machines, 3D printers, and other prototype production equipment
Strong analytical skills with experience using data analysis software (e.g., Excel, Python, Power BI, etc.) to drive improvements in machine shop operations
Proven track record of optimizing operations and driving cost reductions while maintaining high-quality standards
Experience with CAD/CAM software and other relevant design and manufacturing tools
Programming with MasterCam for standard and model base definition
Knowledge of lean manufacturing principles, Six Sigma, or other process improvement methodologies
Excellent communication and leadership skills, with the ability to collaborate effectively with cross-functional teams
Advanced certification in data analytics, Six Sigma, or lean manufacturing is preferred.
Familiarity with rapid prototyping and additive manufacturing techniques is preferred.
Strong understanding of the current machining practices, tooling, equipment, technology, and trends is preferred.
Strong understanding of common manufacturing processes (EDM, waterjet, laser cutting, welding, and sheet metal fabrication) is preferred.
Experience working with union employees is preferred.
Must possess excellent customer service skills.
Must be able to communicate effectively and professionally with internal customers and vendors.
Required Education:
Bachelor’s degree in mechanical engineering, industrial engineering, or related field, or an equivalent combination of degree and years of experience in machining and machine shop operations.
Special Requirements:
U.S. citizen or permanent resident status required.
Able to work flexible hours
Compensation:
The base salary range for this full-time position is $109,695 - $137,145 + bonus + benefits.
Our salary ranges are determined by role, level, and location. The range displayed on each job posting reflects the minimum and maximum target for new hire salaries for the position. Within the range, individual pay is determined by work location and additional factors, including job-related skills, experience, and relevant education or training. Your recruiter can share more about the specific salary range during the hiring process. Please note that the compensation details listed reflect the base salary only, and do not include potential bonus or benefits.
Top Skills
What We Do
HRL Laboratories, LLC, Malibu, California, (hrl.com) pioneers the next frontiers of physical and information science. Delivering transformative technologies in automotive, aerospace and defense, HRL advances the critical missions of its customers. As a private company owned jointly by Boeing and GM, HRL is a source of innovations that advance the state of the art in profound and far-reaching ways.
Why Work With Us
Our success is the result of our collaborative team of researchers, many of whom are the leading experts in their fields. Through their insights in support for our customers, we are finding the unique opportunities in technology.
Gallery
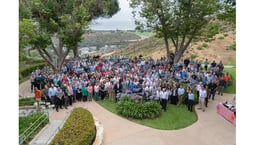
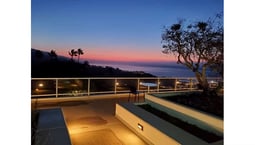
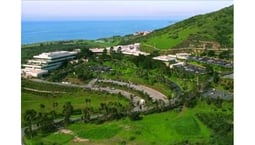
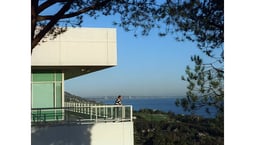
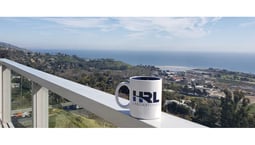
HRL Laboratories Offices
Hybrid Workspace
Employees engage in a combination of remote and on-site work.
Hybrid Policy is role specific.