Role Summary
- Provide Formulation and filling equipment engineering subject matter expertise for Pfizer's state-of-the-art, large scale injectables facility located in Vizag, India
- The equipment engineer is responsible for providing engineering technical and equipment qualification support to the operating unit ensuring that the equipment is running as intended and that all equipment issues are resolved to support the manufacture and timely disposition of product
- This role focuses on leading and resolving technical issues within the Operations Unit, implementation of CAPAs and equipment improvements, support generation of product impact assessments, providing routine technical support and troubleshooting, investigation closeout and maintaining the qualification status of the physical plant and equipment
- The Equipment Engineer is responsible for Project Management/ execution of assigned projects (short duration), which includes the management of internal company resources (assets financial and personnel), external Engineering and vendors as part of the execution of projects. The direct management responsibility includes all support activities and functions necessary to ensure successful completion of project objectives
- The Equipment Engineer is responsible for providing technical expertise during audits and to present/ defend engineering systems, applicable change controls, investigations and equipment qualification packages to the regulatory agencies if required
- Support development of a world-class sterile injectables manufacturing site at Vizag by providing Equipment Engineering and Technology expertise
- The scope of equipment includes: Solution and emulsion preparation equipment's and filling lines.
ROLE RESPONSIBILITIES
In order of importance, indicate the primary responsibilities critical to the performance of the role. It is recommended not to list actual tasks but focus on 5-8 key result areas that highlight accountability and level of judgment required.
Key Areas
Activities
Equipment Qualification /Maintenance
- Provide technical support in periodically reviewing Preventive/Predictive Maintenance programs, in collaboration with the maintenance manager, to improve the operational reliability of the equipment
- Ensure all equipment installed is safe, effective and in compliance with industry standards
- Provide routine equipment technical support and troubleshooting for resolution of manufacturing issues
- Work with the Maintenance and operation managers to develop competency improvement projects and tasks to up-skill the Manufacturing and Technician teams.
- Support assessing training requirement of the Maintenance and Manufacturing operators and develop, in collaboration with the OEMs as required, appropriate and tailored training plan. Provide technical training on process and equipment in collaboration with OEMs, as required
- Own the relationship with key vendors for the assigned equipment through this relationship speed up troubleshooting and faultfinding responsiveness, improve equipment and spares availability through the equipment lifecycle
- Own the equipment drawings, P&ID's, and act as the primary link into the Automation team for the assigned equipment sets
- Work with the Reliability Engineer to get source data on equipment performance with a view to driving system improvements
- Support the design and selection of process & ancillary equipment.
- Responsible to coordinate Investigation & CAPA manager (tracks and manages the investigations, CAPAs; coordinate with other cross functions), Automation & Instrumentation lead (owns administration of automation systems, and manage instrumentation SMEs), Plant Engineering lead (leads the maintenance and calibration of infrastructure inside TS Block, owns reliability program), Engineering PMO (program management for all engineering related activities), Capital Projects lead (manage the site capital program)
- Responsible to Coordinate with Global Functions, Equipment engineering SME's, Process Engineering SME's, Automation SME's.
Project /Finance Management
- Capacity and Reliability improvement projects delivered on time, within cost and meet the specifications/requirements of the Operating Unit.
- Undertake continuous improvement projects to improve the performance or output of the assigned equipment: Identify equipment improvement and develop these into project scopes, this may also include progressing to funding approvals.
- Lead/ represent Formulation Equipment engineering on short duration project teams where responsibilities would include SME technical oversight and the management and resolution of technical issues or changes arising throughout the project lifecycle whilst ensuring overall project objectives of scope, cost and schedule are adhered to.
- Financial Accountability to support generation of site capital budget by proposing appropriate technology solutions
Reporting
- Trend the breakdowns /concerns of the equipment and implement corrective actions to improve the reliability of the equipment.
Documentation/Compliance
- Ensure all company and site engineering policies and procedures are adhered to.
- Lead major investigations into equipment and/or process failures and implement equipment CAPA and performance improvements.
- Review and approve documentation for cGMP validation, requalification and periodic review of systems, equipment & manufacturing processes, including validation plans, risk assessments, protocols, and reports to maintain the equipment in a validated state
- Write product/process impact assessments in support of investigation closures
- Review all documents in relation to all improvements and upgrades
- Own and implement Change Controls and assigned CMTs
Cultural Attributes
- Conduct himself/herself in line with the Pfizer Values; Courage, Equity, Excellence & Joy
Statutory Obligations
- Provide technical expertise during audits and to present/ defend engineering systems, applicable change controls, investigations and equipment requalification packages to the regulatory agencies if required.
- Conduct himself/herself in line with relevant legislation pertaining to workplace health and safety, discrimination, harassment, and bullying.
Environmental Health and Safety
- Participate in and take responsibility for workplace environment, health and safety at the level required for this position, following the guidelines in the company Environmental, Health and Safety Management System Manual.
- Ensure that all safety instructions and measures are strictly observed.
- Conducting Safety Assessments
ESSENTIAL REQUIREMENTS
Determines the education, experience and competencies that a person needs to have in order to do the job effectively
Preferred Education/ Qualification (Eg. Diploma, Certificates, bachelor's degree, Master's Degree, licenses, technical certification)
- Bachelor's degree in Engineering (Mechanical / Chemical / Electrical / Instrumentation)
Experience (type and length of experience needed to perform effectively)
- 5-10 years of experience in fill finish (injectables) pharmaceutical industry
Core Competencies (refers to skills, knowledge and attributes that an employee must possess to be competent in the position
Detailed knowledge of the following:
- Knowledge and understanding of the US cGMP (21 CFR Parts 210, 211)
- Understanding of the local safety and environmental regulations
- Understanding of electronic batch records and electronic signatures (21CFR Part 11)
- Ability to communicate with site & corporate global functions
- Well versed with industry best practices and guidelines such as those with ISPE, PDA, ASME, etc.
Standards, Processes & Policies
- Good Automated Manufacturing Practice guidelines for validation of automated systems
- Basic HSE and GMP/QA knowledge
- Knowledge on Clean room requirements, behavior, Good documentation work and Regulatory Guidelines
DESIRABLE REQUIREMENTS
Identify the 'nice to haves'. These are not critical but would be advantageous.
Advanced Competencies (Up to 5 advanced competencies can be list)
- Documentation Preparation and review skills
- Effective problem-solving capabilities
- Excellent Interpersonal, written and communication skills
- Effective coordination between departments
Additional Desirable Requirements (may be experiences, courses, skills etc)
None
DECISION MAKING SCOPE
Describes the level of authority the employee has in the areas of financial, colleague and policy/procedures.
Staffing (Responsibilities such as recruitment, training, performance reviews, coaching)
(for people managers only)
☐ Recruitment ☐ Performance Review
☒ Training ☒ Coaching ☐ Not applicable
Work Location Assignment: On Premise
Pfizer is an equal opportunity employer and complies with all applicable equal employment opportunity legislation in each jurisdiction in which it operates.
Engineering
#LI-PFE
What We Do
Our purpose ensures that patients remain at the center of all we do. We live our purpose by sourcing the best science in the world; partnering with others in the healthcare system to improve access to our medicines; using digital technologies to enhance our drug discovery and development, as well as patient outcomes; and leading the conversation to advocate for pro-innovation/pro-patient policies.
Why Work With Us
We are the inventors, the problem solvers, the big thinkers — those who surmount any hurdle to deliver breakthrough medicines to the people who are counting on them the most.
Gallery



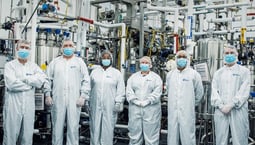

Pfizer Offices
Hybrid Workspace
Employees engage in a combination of remote and on-site work.