At John Deere, we run so life can leap forward. This powerful purpose is our promise to humankind that we will dream, design, and deliver breakthrough products that sustain our world for generations to come. The world is counting on us to feed billions of people and build vital infrastructures in villages, towns and megacities. And we live up to the legacy our founder forged in a one-room blacksmith's shop nearly two centuries ago by creating a culture that brings out the best in all of us. A culture where great ideas thrive because every voice is heard.
Title: Manufacturing Engineer - 110875
Primary Location: Canada (CA) - British Columbia - Langley
Function: Factory Engineering (CA)
Onsite/Remote: Onsite Position
Candidates applying for this position must be legally eligible to work in Canada.
Your Responsibilities
As a Manufacturing Engineer for John Deere Specialty Products located in Langley, BC, you will be responsible for enabling our assembly, paint, and material handling operations to produce high quality forestry tracked equipment, safely and efficiently. In addition, you will:
- Review Engineering BOMs, 3D models and quality specifications in order to translate the intent and expectation of the product design into the manufacturing process
- Use digital tools like Creo, NX, VisView, SAP, MPPlanner, ACAD and Microsoft PowerPoint to create work instructions that effectively communicate how to assemble hydraulic, structural, and electrical components at a production pace
- Proactively promote and support continual improvement activities to enhance the quality system, such as 5S, Kaizen, SCR's, etc
- Implement cost effective tooling solutions for the Assembly, Paint and Material Handling teams by sourcing purchased products or developing custom designs
- Work with the Supply Management and Material Handling teams to develop effective logistics plans for delivering the material to the Assembly Line
- Establish routings, Sequence of Events (SOE), line balances, layouts, tooling, assembly costs, Operator Method Sheets (OMS) and control plans for revisions to current operations or PDP programs.
- Address quality issues by utilizing root cause analysis and mistake proofing by gathering and analyzing data; work with design, quality, advanced technologies, maintenance, and other functional areas to resolve issues.
- Support the analysis, development, and implementation of new manufacturing processes and technology aligned to the Smart Connect Factory strategy
What Skills You Need
- Experience in a manufacturing environment with proficient knowledge of assembly processes, quality, tooling and safety
- Good communication skills and demonstrated ability to work effectively with salaried and wage union personnel in a team environment
- Experience with shop floor documentation (Sequence of Events, Labor Standards, Operator Methods Sheets and Line Balancing (DLBT)
- Experience in project management and business planning for small tactical projects and/or large strategic projects
- Self-motivator with the ability to execute a variety of tasks with little supervision
- Experience with line design, material presentation, cycles of imbalance and visual management tools, such as simulations and 3D factory
- Experience teaching and mentoring less-experienced Engineers or Engineering Coop students
- 2 plus years of related manufacturing experience
What Makes You Stand Out
- Experience in troubleshooting and repairing industrial equipment, vehicles, or heavy equipment
- Experience supporting engineering projects in a factory, warehouse, and/or industrial environment
- Experience with AutoCAD, Creo and SAP
- Experience working with programming languages such as SQL, Python, R, Java, VBA or similar
- Experience with John Deere Specific manufacturing software JDAAT (John Deere Assembly Assist Tool) and MPP (Manufacturing Process Planner)
Education
- Mechanical, Manufacturing, Industrial, Electrical or Mechatronics Engineering
In accordance with the John Deere Accommodation Policy, reasonable accommodation of any of these qualifications may be considered. An equal opportunity employer, John Deere requires a diversity of people, perspectives and ideas to address the complex challenges of its global business.
This position will be posted for a minimum of 7 business days and unposted when a qualified pool of candidates is achieved.
The information contained herein is not intended to be an exhaustive list of all responsibilities, duties and qualifications required of individuals performing the job. The qualifications detailed in this job description are not considered the minimum requirements necessary to perform the job, but rather as guidelines.
Top Skills
What We Do
Life can’t evolve without innovation. That’s why we’re ideating to help feed the planet, build smarter, and help our farmers and growers to sustainably optimize their land. The mission is underway, but we need the right people to continue bringing it to life. From coders to assemblers and from engineers and tech experts to marketers and field teams. All find a purpose to drive them, a culture to thrive in, and a world of opportunities.
Why Work With Us
Our company is more than just a place to work. For John Deere employees, it’s where we dream, design, and deliver machines and technology that help feed a rapidly growing world and build critical infrastructure in villages, towns and modern megacities.
Gallery
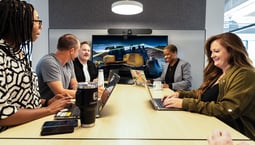
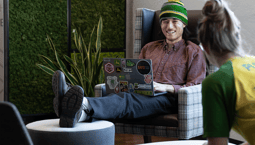
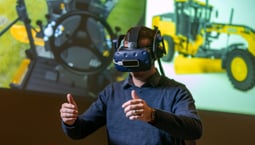

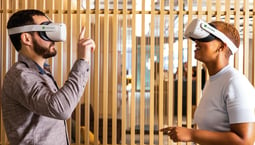
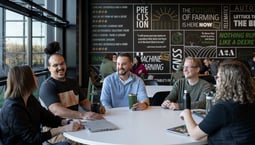

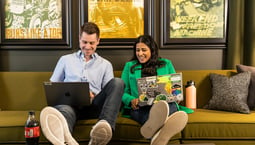
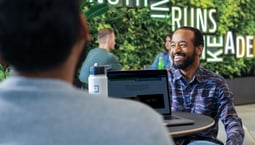
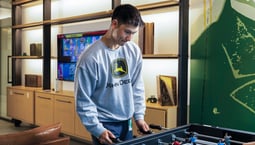
John Deere Teams
John Deere Offices
Hybrid Workspace
Employees engage in a combination of remote and on-site work.