What we offer:
At Magna, you can expect an engaging and dynamic environment where you can help to develop industry-leading automotive technologies. We invest in our employees, providing them with the support and resources they need to succeed. As a member of our global team, you can expect exciting, varied responsibilities as well as a wide range of development prospects. Because we believe that your career path should be as unique as you are.
Group Summary:
The Magna Exteriors portfolio of products includes access systems such as liftgates, exterior trim, modular systems, front-end modules including fascia, active aerodynamic systems and other lightweight structural components for automotive, commercial truck and other industrial markets.
Recognized globally as an innovator in all aspects of vehicle exteriors, Magna provides everything needed, from materials development and design through manufacturing and assembly, to help automakers create sleek, state-of-the-art vehicles across the world.
Job Responsibilities:
Purpose:
Establish a technical lead to develop, execute, and sustain a comprehensive strategy for a safe, efficient, and profitable injection molding business at AIM Systems.
Essential Duties and Responsibilities:
- Specify, procure, and commission new molding equipment for the division. Includes coordination of supporting departments such as maintenance, facilities, tooling, EHS, quality, and operations.
- Define complete injection molding work cell requirements, including tool standardization, machine design & capability (including linkage between barrel and shot size to optimum product manufacturing performance).
- Review part design concepts and provide feedback to support design for manufacture.
- Lead cross-functional team partners to achieve divisional safety, quality, delivery, and operational goals.
- Implements continuous improvements in yield, utilization, cycle time, mold change over times and labor efficiency of the department
- Analyze and resolve process problems as well as initiate and implement cost reduction programs to process technology in molding department
- Stay informed about advancing technologies and processes to support opportunities for continuous improvement, efficiency, and value add.
- Provide technical insight for the development and oversight of a robust preventative maintenance system.
- Supervise reporting personnel by following the principals of the Magna Employee's Charter.
- Oversee initial machine process setup, document all proposals for improved efficiencies and make adjustments as required
- Continually monitor all processes related to injection molding
- Responsible for departmental KOI goals to achieve business objectives related to uptime, part quality, mold change time and cycle time.
- Support all customer quality standards as well as the standards of Magna.
- Analyze data to determine statistics, trends, measurable, etc. and take action as required.
- Develop and implement PFMEA's, Continuous Improvement Plans, Control Plans, and work instructions in the Molding Department.
- Responsible for applying standard engineering principles and analytical techniques to the design and development of the manufacturing processes to ensure continuous improvement efforts and cost reduction activities are exceeding the expectations of Magna and the customer
- Responsible for overseeing all activities related to supporting technical and manufacturing solutions; including engineering and design to achieve goals and objectives relating to research and development, organizational projects and services for continuous improvement and risk reduction.
- Participate in the advanced product quality planning FMEA activities for the development of the control plan for all manufactured parts by the injection molding department
- Responsible for start-up and set-up of new tools and resins, and for conducting tool and resin trials, including documentation
- Analyze and resolve process problems as well as initiate and implement cost reduction programs to process technology in molding department
- Identify growth and development opportunities and on-going training needs for Process Engineers, Technicians, Mold Setters, and Material Handlers, which provide for an overall positive working environment.
- Train, mentor and coach Process Engineers, Process Team Leaders, and Technical Team Members in developing teamwork skills and team-oriented activities in a positive working environment.
- Responsible for the development and implementation of quality standards to ensure compliance to the designated ISO/TS16949 responsibilities, environmental management system and health and safety guidelines. Ensures that systems and processes are identified and any non-conformances are corrected in a timely manner.
- Manage and provide resources and support for continuous improvement activities as they relate to manufacturing processes, safety, product quality and all other functions.
- Lead problem solving activities as they relate to injection molding. Where special actions are necessary, responsible to ensure that all departments involved are properly informed.
- Responsible for maintaining positive employee relations including fostering an open communications climate, effective resolution of employee concerns and consistent application of company policy.
Qualifications:
To perform this job successfully; an individual must be able to perform each essential duty satisfactorily. The requirements listed below are representative of the knowledge, skill, and/or ability required. Reasonable accommodations may be made to enable individuals with disabilities to perform the essential functions.
Education/Special Knowledge:
- Bachelor's Degree, preferably in Plastics, Mechanical, or Chemical Engineering or equivalent combination of education and work experience
Experience:
- Minimum 10 years of experience in a lead technical role within injection molding, preferably in automotive manufacturing
- Minimum 10 years of processing plastics and setting tools
- Knowledge of automation systems, robotics and controls a must.
- Strong problem solving and decision-making skills to deal with issues as they arise.
- Working knowledge of continuous improvement processes/lean manufacturing concepts, methods. and principles.
- Good understanding of time and motion studies is required.
- Working knowledge of Statistical Process Control, DOE's, Failure Mode and Effects Analysis, Production Part Approval Process, Advanced Product Quality Planning, GD&T, IATF 16949, and 8D
- RJG Master Molder Certification or AIM preferred
- Excellent knowledge of injection molding presses, molds, mold design and other relevant processing equipment such as hoppers/loaders, blenders, dryers, sprue pickers, hot runner systems, etc.
- Knowledge of automation systems and controls
- Demonstrable communication (written and oral), organizational, and leadership skills
- Personal computer skills
Additional Knowledge/Training:
- PC Training
- Problem Solving (e.g. 8D's, etc.)
- Managing the Employee Charter
- Time Management
- Interpersonal Communication
- ISO/TS16949:2002
- Hazardous Communication
- Performance Management
- Personal Protective Equipment
- Ergonomics
- Bloodborne Pathogens
- Safety Signs
- Lockout/Tagout
- Confined Space
- Pedestrian Safety
- Emergency Evacuation
- 18001 Awareness
- 10 Hour OSHA Training
Physical Demands:
The physical demands described here are representative of those that must be met by an employee to successfully perform the essential functions of this job. Reasonable accommodations may be made to enable individuals with disabilities to perform the essential functions.
- May be required to stand and/or sit in excess of 6 hours per day
- May be required to lift, push and/or pull 40 pounds
- Average mobility to move around a manufacturing environment
- Able to conduct normal amount of work at a computer
- May require travel
Awareness, Unity, Empowerment:
At Magna, we believe that a diverse workforce is critical to our success. That's why we are proud to be an equal opportunity employer. We hire on the basis of experience and qualifications, and in consideration of job requirements, regardless of, in particular, color, ancestry, religion, gender, origin, sexual orientation, age, citizenship, marital status, disability or gender identity. Magna takes the privacy of your personal information seriously. We discourage you from sending applications via email to comply with GDPR requirements and your local Data Privacy Law.
Worker Type:
Regular / Permanent
Group:
Magna Exteriors
What We Do
We are a mobility company that innovates like a start-up and thinks like a technology company. This helps us anticipate change in one of the most complex industries in the world and respond quickly. We depend on a team of 171,000 dynamic, entrepreneurial-minded employees in an environment where great ideas flourish. Our presence spans 343 manufacturing operations and 88 product development, engineering and sales centers in 29 countries.
We understand that you need a career as unique as you are. Whether you want to advance your existing expertise or try something completely different, we are committed to your growth.
Why Work With Us
At Magna, our engineering team is advancing mobility for everyone and everything. Joining this team means being a part of the design, development, and manufacturing of the world’s most advanced mobility technology. Innovations that move families, shape communities, and improve lives. You can follow your passions and shape your own career path.
Gallery
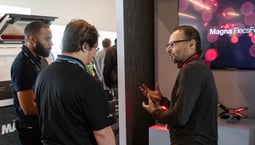
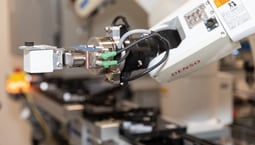
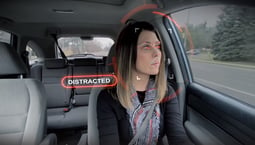
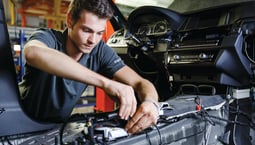
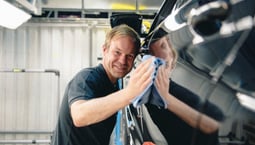
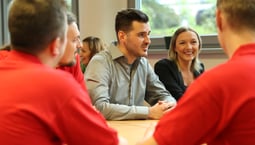
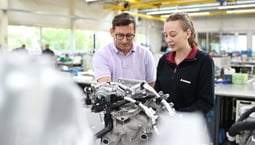
Magna International Teams
Magna International Offices
Hybrid Workspace
Employees engage in a combination of remote and on-site work.
Majority of roles are hybrid with flexibility. Please speak with our recruiting team for specific details on hybrid work.