What we offer:
At Magna, you can expect an engaging and dynamic environment where you can help to develop industry-leading automotive technologies. We invest in our employees, providing them with the support and resources they need to succeed. As a member of our global team, you can expect exciting, varied responsibilities as well as a wide range of development prospects. Because we believe that your career path should be as unique as you are.
Group Summary:
Cosma provides a comprehensive range of body, chassis and engineering solutions to global customers. Through our robust product engineering, outstanding tooling capabilities and diverse process expertise, we continue to bring lightweight and innovative products to market.
Job Responsibilities:
This job description in no way implies that these are the only duties to be performed in this position. Associates will be required to follow any other job-related instructions or to perform other job duties requested by their manager.)
1. Ensure that operator safety devices function properly.
2. Ability to perform electrical diagnosis, recommend repair or repair as needed.
3. To work in a safe, quality minded and productive manner with a sense of urgency to achieve maintenance deadlines and to attain production priorities as scheduled.
4. Support goal of achieving first time quality and efficiency.
5. Maintain accurate documentation resulting in shared knowledge of issues and lessons learned.
6. Troubleshoot and train others on identifying root causes of equipment failures.
7. Oversee all upgrades and programming changes.
8. Ensure that line is built in accordance with all aspects of the latest version of the LMV Automotive Systems build standards.
9. Utilize good working knowledge of all technologies used in the development and build of automated assembly lines.
10. Ensure effective deployment of all available resources.
11. Develop and implement innovative solutions to manufacturing issues related to product development or enhancement.
12. Evaluate and make recommendation on equipment updates.
13. Troubleshoot programming failures and adjusts as necessary.
14. Evaluates and makes recommendations on new equipment.
15. Sets up new programs, PLC ladder logic, robot interfacing and documentation.
16. Implements improvements in cycle time of robotic welding and assemblies.
17. Trains personnel in the use of robot interfacing and PLC ladder logic.
18. Follows and supports LMV Automotive Systems' and Magna's operating principles.
19. Supports efforts to achieve department and plant goals on Employee Opinion Survey.
20. Works with vendors and/or contractors, displaying company's core values.
21. Communicates with maintenance manager and maintenance area/shift leaders and other plant personnel about maintenance concerns, providing complete action plans and status reports as and when required.
22. Work with production and other departments on basic troubleshooting and corrections for everyday issues.
23. Complete correspondence, forms and reports using personal computer and required software.
24. Obtain and attend training for professional development and to stay current on maintenance and safety requirements and other training as required.
25. Handle confidential information on a regular basis.
Performs other duties as assigned.
Supervisory Responsibilities:
Has a responsibility to help develop all maintenance apprentices and give guidance where needed.
Qualifications: (These qualifications represent the minimum requirements of the position. Associates will be required to possess the ability and aptitudes to perform the duties proficiently.)
Education and/or Experience:
- High school diploma or GED
- Two- or four-year degree in Electrical Engineering or related field and/or 4 years job related experience
Knowledge, Skills, and Abilities:
- Understanding of metal stamping, spot welding and assembly processes.
- Complete understanding of PLCs and programming with the ability to program/teach robots.
- Electrical knowledge (National Electrical Code) and control wiring.
- Excellent interpersonal skills to develop positive relationships with associates, customers, and vendors.
- Proficient computer skills required.
- Ability to communicate with others, both verbal and written.
- Able to prepare, read, write, and interpret reports, instructions, procedures and business correspondence.
- Able to respond to questions clearly and effectively from management and customers.
- Must have good organizational skills.
- Must exhibit high integrity and honesty.
- Ability to read, write, analyze, and interpret technical procedures, blueprints, diagrams, requirements, and business correspondences.
- Ability to effectively and appropriately present information and respond to questions from various groups.
- Ability to apply advanced mathematical concepts as appropriate.
- Ability to define problems, collect data, establish facts, and draw valid conclusions.
- Must have good organizational skills.
Physical Demands
- Must be able to perform physical activities, such as, but not limited to, lifting equipment (up to 40 lbs. unassisted), bending, standing, climbing, or walking.
- Must be able to safely use manual tools and power equipment common in the construction trades.
- Must be able to handle hazardous materials safely and tolerate exposure to electrical and other environmental hazards.
Environmental Conditions:
- Must be able to work in various locations within and outside the manufacturing plant.
- Must be able to rotate working shifts and weekend overtime to meet department requirements with a minimum amount of supervision.
- Exposed regularly to elements such as temperature and noise.
- Safety precautions to be observed in the maintenance and installation of electronic and mechanical equipment.
- Must be comfortable with working at heights and within confined spaces.
Environmental, Health & Safety:
- Support and comply with all TS16949 & ISO14001 procedures and work instructions.
- Support a safe and healthful work environment that is free of recognized hazards for all employees, contractors, and visitors.
- Cooperate with all local, state, and federal agencies, such as OSHA or the EPA, in the event of an inspection.
- Know and follow all applicable EH&S Policies and Procedures.
Awareness, Unity, Empowerment:
At Magna, we believe that a diverse workforce is critical to our success. That's why we are proud to be an equal opportunity employer. We hire on the basis of experience and qualifications, and in consideration of job requirements, regardless of, in particular, color, ancestry, religion, gender, origin, sexual orientation, age, citizenship, marital status, disability or gender identity. Magna takes the privacy of your personal information seriously. We discourage you from sending applications via email to comply with GDPR requirements and your local Data Privacy Law.
Worker Type:
Regular / Permanent
Group:
Cosma International
Top Skills
What We Do
We are a mobility company that innovates like a start-up and thinks like a technology company. This helps us anticipate change in one of the most complex industries in the world and respond quickly. We depend on a team of 171,000 dynamic, entrepreneurial-minded employees in an environment where great ideas flourish. Our presence spans 343 manufacturing operations and 88 product development, engineering and sales centers in 29 countries.
We understand that you need a career as unique as you are. Whether you want to advance your existing expertise or try something completely different, we are committed to your growth.
Why Work With Us
At Magna, our engineering team is advancing mobility for everyone and everything. Joining this team means being a part of the design, development, and manufacturing of the world’s most advanced mobility technology. Innovations that move families, shape communities, and improve lives. You can follow your passions and shape your own career path.
Gallery
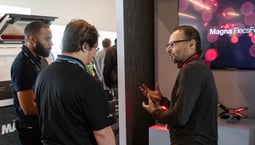
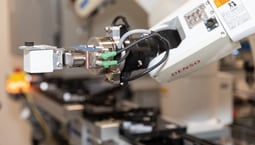
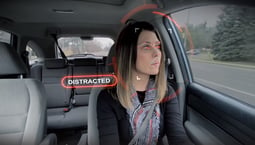
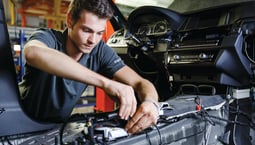
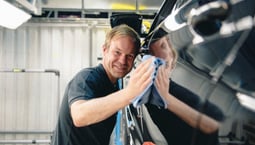
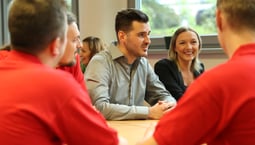
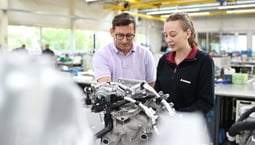
Magna International Teams
Magna International Offices
Hybrid Workspace
Employees engage in a combination of remote and on-site work.
Majority of roles are hybrid with flexibility. Please speak with our recruiting team for specific details on hybrid work.