What we offer:
At Magna, you can expect an engaging and dynamic environment where you can help to develop industry-leading automotive technologies. We invest in our employees, providing them with the support and resources they need to succeed. As a member of our global team, you can expect exciting, varied responsibilities as well as a wide range of development prospects. Because we believe that your career path should be as unique as you are.
Group Summary:
The Magna Exteriors portfolio of products includes access systems such as liftgates, exterior trim, modular systems, front-end modules including fascia, active aerodynamic systems and other lightweight structural components for automotive, commercial truck and other industrial markets.
Recognized globally as an innovator in all aspects of vehicle exteriors, Magna provides everything needed, from materials development and design through manufacturing and assembly, to help automakers create sleek, state-of-the-art vehicles across the world.
Job Responsibilities:
Purpose:
Oversee all activities related to Manufacturing/ Process Controls, installation, documentation and testing activities of all equipment including, but not limited to, robotics, assembly, on-line fixtures, conveyor systems, etc.
Essential Duties and Responsibilities:
- Drive all activities relating to ensuring existing and new equipment is built and running in accordance to specifications. Including the troubleshooting, debugging, start-up and programming of all automated equipment and upgrades.
- Technical expert for electrical controls, program logic controls, robot programming and troubleshooting, vision inspection system programming
- The ability to program or modify HMI's (ex; RS Logix 500 & 5000, Allen Bradley, Siemens, Ignition and Python)
- Determine correct controls for all Poke Yokes (Vision Systems, PLC's, and Robotics).
- Understand logic writing to create handshakes between the equipment and I.T Systems.
- The ability to build and wire control panels
- Keep and update all equipment drawing, electrical prints etc...up to date as changes are implemented.
- Create training materials, as well as, conduct training of support personnel as required.
- Identify and correct any safety issues inside the facility.
- Ensure a safe working environment by observing safe work practices and by following all safety policies and procedures
- Coordinate the development in writing and maintaining effective maintenance specification and preventative maintenance programs on all equipment to ensure top performance for productivity.
- Create training materials, as well as, conduct training of support personnel as required.
- Participate in the design of custom process automation machines, equipment, systems, devices and fixtures to support assembly requirements.
- Recommend equipment improvements and/or manufacturing methods to improve.
- Coordinate all mechanical/electrical system modifications with external vendors, maintenance personnel.
- Support and assist maintenance personnel with diagnosing software and electrical system problems.
- Work closely with production, maintenance and engineering to establish optimized performance of all equipment.
- Support the quote preparation process by reviewing and helping to select appropriate robots for identified robotic applications into existing operations.
- Support the quote preparation process by reviewing and selecting appropriate PLC products.
- Initiate Engineering Change Requests for appropriate equipment changes.
- Assist in the negotiation of contracts with equipment vendors as needed.
- Implement continuous improvement strategies to reduce scrap cost and improve productivity and quality.
- Assists in the preparation and execution of all new program launches, including supporting of all pilot build activities.
- Assist in determining resolutions to customer issues through the implementation of process and design changes as they relate to equipment.
- Assist in the implementation of IATF16949:2016.
- Develop an effective Best Practices process to ensure lessons learned are implemented in new programs and processes.
- Support cost savings activities: problem solving cost saving analysis, root cause analysis, capital payback analysis, process manufacturing analysis, i.e. lean manufacturing MCRP analysis.
- Confers with vendors to determine product specifications and arrange for purchase of equipment, and/or materials supporting continuous process improvements.
- Provide estimate production times, staffing requirements, and related costs to provide information for management decisions in synchronous related matters including simulated trials.
- Must be extremely flexible for off shift availability and representation.
- Investigate new and emerging technologies that may be of interest to Magna Modular Systems.
- Other duties, as assigned.
To perform this job successfully; an individual must be able to perform each essential duty satisfactorily. The requirements listed below are representative of the knowledge, skill, and/or ability required. Reasonable accommodations may be made to enable individuals with disabilities to perform the essential functions.
Qualifications:
Education/Special Knowledge:
- Bachelor's Degree in Engineering or related field; or equivalent combination of education and 4 years' experience.
Experience:
- Minimum 3 years' experience with automated equipment in a manufacturing environment
- Minimum 3 years' experience PLC programming.
- Solid understanding of principles used in multi-axis robotic systems, conveyor transport systems.
- Strong "hands-on" capability in the installation and programming robotic and PLC controls systems in a manufacturing environment.
- Demonstrated oral and written communication skills; customer focused.
- Strong computer skills.
- Understanding of manufacturing, assembly, sequencing and equipment principles.
Additional Knowledge/Training:
- PC Training
- Problem Solving (e.g. 8D's, etc.)
- Employee Charter
- Time Management
- Interpersonal Communication
- IATF16949:2016
- Hazardous Communication
- Performance Management
- Personal Protective Equipment
- Ergonomics
- Bloodborne Pathogens
- Safety Signs
- Lockout/Tagout
- Confined Space
- Pedestrian Safety
- Emergency Evacuation
- 18001 Awareness
- PLC Programming
Health and Safety Requirements:
Provide administrative support to the Company health, safety and environmental objectives and support the company's health and safety directives to provide a safe and healthful workplace for all employees, this includes:
- Ensure a safe working environment by observing safe work practices and by following all safety policies and procedures.
- Regulatory compliance with local, state and federal legislations.
- Establishing plant-wide measurable and goals that meet or exceed industry standards, and are monitored, tracked and audited on a regular basis and communicated to employees.
- Recognition of accomplishments/milestones in the areas of safety, environmental, ergonomics and employee wellness.
- Development of effective programs that increase employee awareness and involvement in the areas of safety, environmental, ergonomics and employee wellness.
- Accountability of supervisors for enforcing safety rules and implementing the necessary training and corrective actions to ensure proper focus on established objectives.
Physical Demands:
The physical demands described here are representative of those that must be met by an employee to successfully perform the essential functions of this job. Reasonable accommodations may be made to enable individuals with disabilities to perform the essential functions.
- May be required to stand and/or sit in excess of 6 hours.
- May be required to lift, push and/or pull 40 pounds.
- Average mobility to move around a manufacturing environment.
- Able to conduct normal amount of work at a computer.
- May require travel.
Awareness, Unity, Empowerment:
At Magna, we believe that a diverse workforce is critical to our success. That's why we are proud to be an equal opportunity employer. We hire on the basis of experience and qualifications, and in consideration of job requirements, regardless of, in particular, color, ancestry, religion, gender, origin, sexual orientation, age, citizenship, marital status, disability or gender identity. Magna takes the privacy of your personal information seriously. We discourage you from sending applications via email to comply with GDPR requirements and your local Data Privacy Law.
Worker Type:
Regular / Permanent
Group:
Magna Exteriors
Top Skills
What We Do
We are a mobility company that innovates like a start-up and thinks like a technology company. This helps us anticipate change in one of the most complex industries in the world and respond quickly. We depend on a team of 171,000 dynamic, entrepreneurial-minded employees in an environment where great ideas flourish. Our presence spans 343 manufacturing operations and 88 product development, engineering and sales centers in 29 countries.
We understand that you need a career as unique as you are. Whether you want to advance your existing expertise or try something completely different, we are committed to your growth.
Why Work With Us
At Magna, our engineering team is advancing mobility for everyone and everything. Joining this team means being a part of the design, development, and manufacturing of the world’s most advanced mobility technology. Innovations that move families, shape communities, and improve lives. You can follow your passions and shape your own career path.
Gallery
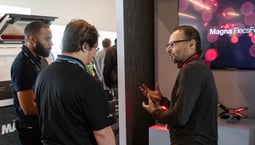
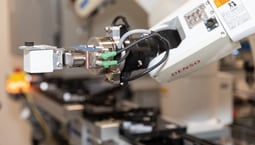
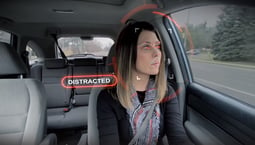
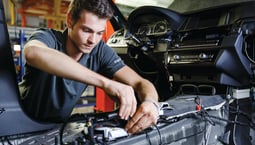
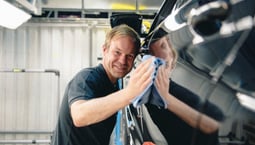
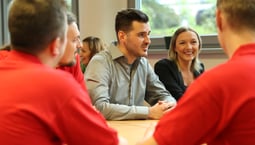
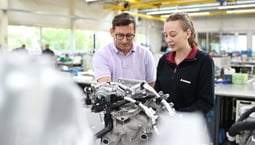
Magna International Teams
Magna International Offices
Hybrid Workspace
Employees engage in a combination of remote and on-site work.
Majority of roles are hybrid with flexibility. Please speak with our recruiting team for specific details on hybrid work.