Imagine a jacket that can light up on night-time walks, heat up electrically on particularly cold days, and have a built-in touch panel used to control your smart phone. Oh, and if you forget it on the train, you can track it down in an app.
This futuristic jacket may be designed by a brand you know, but it could likely be built with technology from Loomia: a New York-based electronic textile firm known today for making the components used in heated car seats, lighting construction workers’ safety jackets, smart vests for factory workers and much more.
E-textiles have actually been around for a while, but before Loomia, they were often too rigid, expensive or hard to produce, said Founder Madison Maxey.
“We just kept iterating and developing and trying new things.”
“We really took a very design-process approach to it,” Maxey said. “We just kept iterating and developing and trying new things, more so than an engineering approach, where you have a spec and you try and meet that spec.”
We spoke with Maxey about how Loomia’s tech is made.
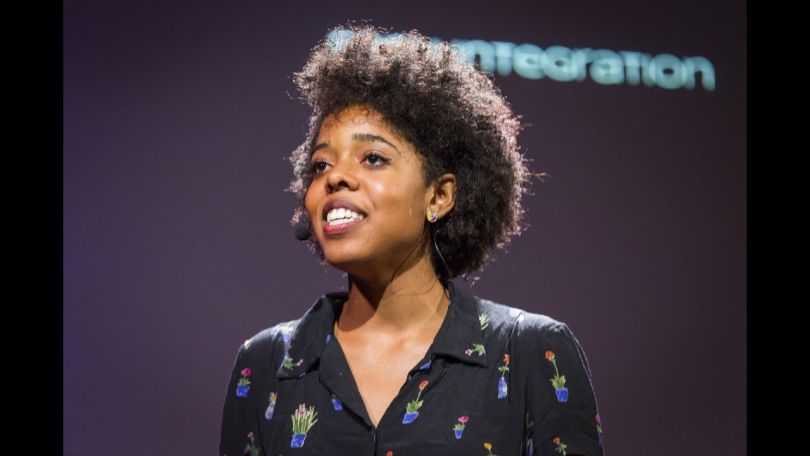
Here’s how it works
Loomia’s Electronic Layer is embedded with electrical circuits and laminated onto fabric. Loomia can heat, light and make fabrics sensitive to touch. The firm works with businesses to create pre-cut patterns of its e-textile that companies then sew onto their products. All of Loomia’s e-textiles connect to an external battery.
Its customers are divided equally in the transportation, healthcare, and outdoor product sectors.
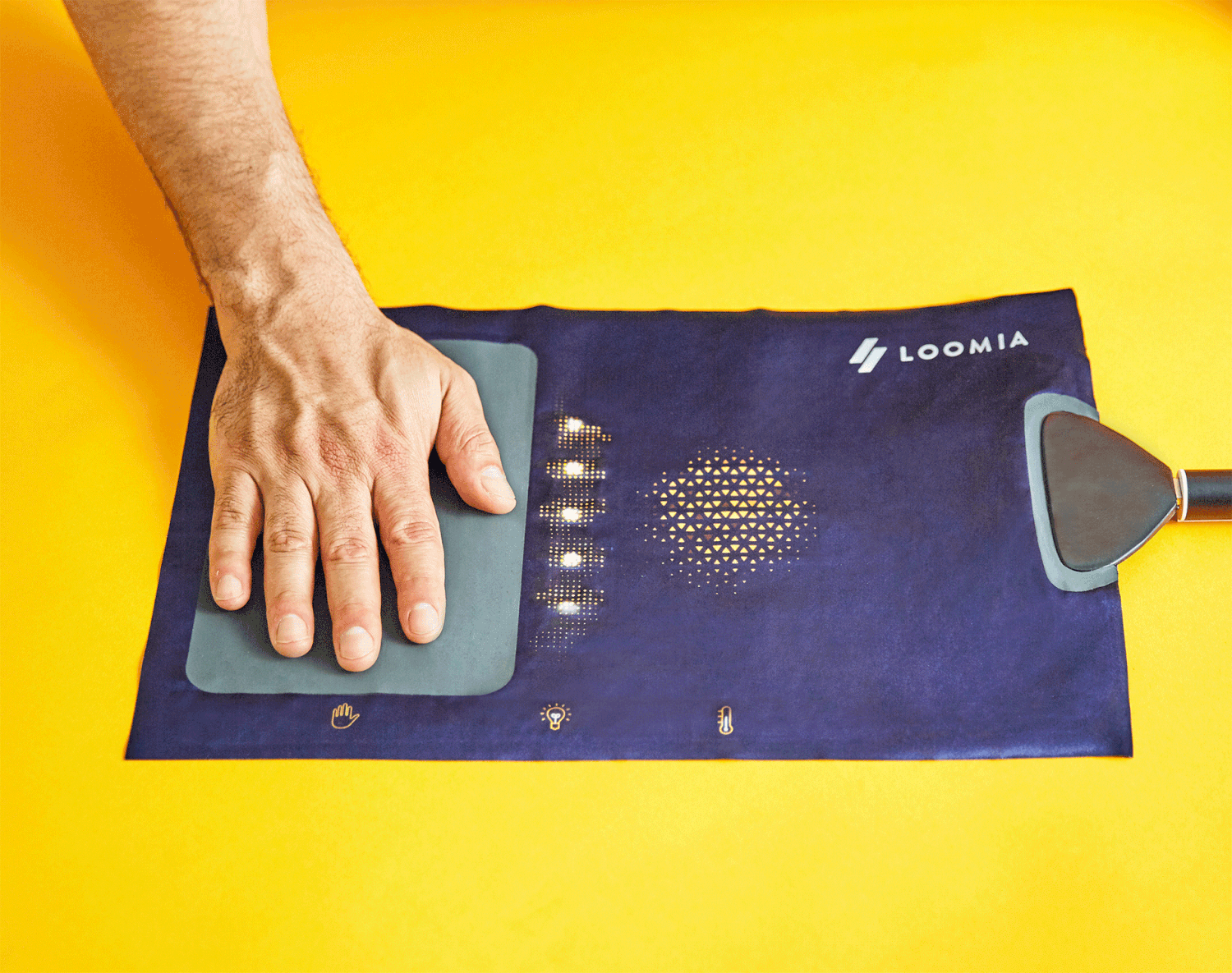
To create an e-textile, makers must pattern a conductive material — like a copper wire that an electric charge can pass through — onto the product. These materials are generally printed, woven, knit or laminated onto the textile, Maxey said.
Initially, Maxey thought printing conductive ink on the textile would be the best way to go, since using conductive ink would allow her to connect the electrical circuits without wires. She started experimenting with conductive ink when she served as the artist-in-residence at Autodesk — a Bay Area tech firm.
At Autodesk, Maxey worked with a chemist to develop a conductive ink that mixed silver nanoparticles and elastic to make a liquid. The two used a CNC printer to print the ink onto fabric, and the resulting textile carried a charge strong enough to make an LED lamp glow. But Maxey had concerns over the ink’s long-term durability.
“When it came to actually scaling it, and differentiation on the market, we decided it wasn’t the best,” Maxey said. “I don’t know if it would last 10 years if it was actually in someone’s product.”
Maxey, along with Loomia Chief Technology Officer Ezgi Ucar, started testing different materials and methods to make e-textiles. She tried knitting circuits into fabric, which required an expensive, hard-to-use digital knitting machine to input a conductor onto the textile. Knitting represented a viable option since it left the resulting fabric soft and comfortable for skin, Maxey said, but the expertise limitations around how to use the equipment and complex circuitry requirements left much to be desired.
Maxey turned to weaving. Weaving e-textiles requires users to weave in a parallel, 90 degree, orthogonal nature so electrical lines can eventually be incorporated into the product. But weaving in such a manner makes it hard to incorporate antennas, which tend to coil in on themselves, Maxey said.
That left laminate as the best option, which is what Loomia uses today to create its tech. Maxey declined to disclose exactly how the firm adds its laminated circuits to e-textiles, but in general, this process works by layering and laminating circuits onto fabric. Maxey said the firm makes custom circuits to address each of Loomia’s functionalities, which include heat, light and touch sensitivity.
Collecting data through interwoven sensors
Loomia is working on creating a Tile tag, with The Tomorrow Lab building the hardware and Fueled powering its software system. It has also embedded sensors in the e-textile to collect data on the frequency of wear, location, level of activity and temperature of the wearer of the clothes. That data is then stored in the Tile and can sync with the blockchain-based Loomia Data Exchange. Users can download the Android mobile app to retrieve and organize their data.
In 2017, Loomia held a token sale through Tile, allowing consumers to purchase the product with Ethereum cryptocurrency. Eventually, the firm hopes to enable consumers to sell their data anonymously to clothing manufacturers looking to supplant their product development cycles through the Tile. Customers would be able to use Ethereum to cash in on digital rewards via Loomia’s Tile.
Maxey said the Tile is currently being marketed to Loomia’s business customers.
“The main hardware is there, so now it’s in the sales process, and we’re getting it out there,” she said.
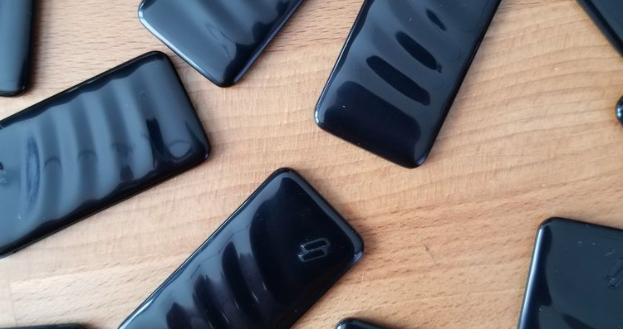
Fashion and tech intersect
After finishing one semester at Parson’s School of Design in New York, Maxey took a leave of absence to enroll in classes at General Assembly because she wanted to learn how to build websites. There, she completed a work study program where she worked in an entrepreneurship coworking space, which gave her access to inspiring entrepreneurs.
“My personal interest in fashion was working with textiles and different teams and materials and different kinds of machines... I think that’s a similar mindset that makes you interested in how technology is built.”
“My personal interest in fashion was working with textiles and different teams and materials and different kinds of machines, very much so into the garment production process,” Maxey said. “I think that’s a similar mindset that makes you interested in how technology is built, like hardware and software and mechanical objects.”
Maxey finished her courses at General Assembly, and went on to eventually receive a $100,000 grant from the Thiel Fellowship. She was the first fashion student to ever earn the recognition. She used the cash to start The Crated, a design studio that partnered with the New York-based Strong Arm Technologies to build harnesses that monitor factory workers’ biometrics to make sure they lift items safely, among other things. She also built an LED matrix dress for designer Zac Posen, and built prototypes for Google and North Face.
She realized the main issue stopping these products from scaling was finding — and affording — a soft, flexible circuit material. Her focus turned to e-textiles, and she renamed her studio Loomia.
“I really wanted to make this product. I wanted to change the foundational technology,” Maxey said.